Più di 100 anni di progresso tecnico ci hanno resi leader nei settori degli Inverter, dei servoazionamenti, della tecnologia di controllo e della robotica.
Automated paper cutting system from baumannperfecta with SLIO control technology and Motoman robot
As a manufacturer of processing machines for the graphics industry , the German Baumann Group is driving the automation of the printing industry through their innovative solutions. A current example are the robotic cutting systems under the baumannperfecta brand, in which the company implements with a Motoman GP50 and SLIO control technology from Yaskawa.
- Industrie
- Printing | Paper | Tissue
- Applicazioni
- Material Handling
- Client
- Baumann Perfecta
- Prodotti
- GP50 - Serie GP
- SLIO
Precision handling for paper – a “delicate natural product”
As it was clear to see from this year's Drupa trade fair, the graphics industry is under pressure to improve its efficiency in the face of a shortage of skilled workers on the one hand and increasingly demanding market conditions on the other. One solution for this is automation in the printing and finishing industry which offers the additional advantage of relieving employees of physically strenuous activities. For example, very heavy paper stacks previously had to be handled manually.
Despite this, the automation of workflow tasks has been slow to take hold in printing businesses, especially where the post-print process is concerned. One reason for this reluctance is the nature of the industry-specific material, namely paper. Because paper is sensitive to environmental conditions such as humidity, it poses particular challenges, as Markus Frick, Managing Director of the Baumann Group, explains: “Since the printing industry requires large weights to be moved with high precision, automation offers very high potential. At the same time, it is difficult to automate the handling of paper, because paper is a delicate natural product.”
With its systems under the baumannperfecta brand, the manufacturer based in Solms, Hesse, has successfully accepted this challenge for years: “We are among the first providers to develop solutions for the automation of cutting and feeding processes in the printing industry,” says Markus Frick, describing the manufacturer's pioneering role. Automation is necessary because the printing and finishing industry faces an increasing shortage of skilled workers and in order to relieve employees of physically demanding tasks – such as the manual loading of heavy paper stacks.
The key to baumannperfecta’s leading position lies its unique know-how: As much as one fifth of the workforce is involved in research and development. The level of vertical integration for baumannperfecta systems, which are designed and built exclusively in Germany, is around 80 percent. And in addition, the Baumann Group – as the first company in the industry – has been creating a technological advantage by the integration of robots in its products for the last eight years.
The only fully automated jogging and cutting system worldwide
A central element of the baumannperfecta portfolio is the world's first – and to date only – fully automatic jogging and cutting system for processing in label production, package printing or classic commercial printing. This modular and scalable system combines a latest generation BASA evolution jogging machine with a robot-supported cutting system. This ensures very high quality of the subsequent print product throughout all the workflow steps – from the creation of the layers, through the aeration and the precise alignment of the press sheets to the final precise and accurate cutting process.
The robust basic design of the cutting machine ensures smooth running and precise cutting results. At the heart of the cutting system is an integrated robot, which is equipped with a gripper system specifically developed by Baumann for paper processing. This takes over the tasks of a human operator before and after the actual cutting process. Specifically, this means gripping, aligning, turning and knocking the pile, as well as transferring the cut paper stacks to an intermediate buffer or unloader. These steps no longer require any manual intervention and they are at the same time carried out with high precision. The automation also makes a 3-shift operation possible, for maximum utilization of the system. The components are designed for continuous use, so that the cutting machines can be used around the clock.
Interoperable control technology from Yaskawa
A complex modular system design of this kind requires a correspondingly powerful control concept. In this specific case, this meant a manufacturer-independent overall solution, as Managing Director Markus Frick explains: “The controller is the heart of our system – not just for us as a manufacturer, but also for our customers. Interoperability plays a central role in this context.” The BASA module is already based on predecessor models with respective third party control equipment. However, this new generation of robot-assisted cutting systems demanded new functionalities, for example with regard to measuring accuracy. The cutting system should also offer the option of being fitted with an additional control unit for fast access to all parameter data at any time. In addition, the controls of the cutting machine and the robot should be designed for very simple, intuitive operation via a touchscreen.
The proven SLIO control and I/O system from Yaskawa met all these requirements for the cutting system and it provided the desired accuracy. With a combination of CPU and matching I/O system as well as a fast backplane bus (at 48MBit/s), it combines highest levels of functionality with a clever mechanical concept in an extremely compact and maintenance-friendly design. Single-channel diagnostic LEDs and standing wiring facilitate commissioning and ensure ease of use for operation and maintenance. A Smart Panel from the Yaskawa portfolio and a remote maintenance module for checking the machine status and providing servicing information round off the features of the system.
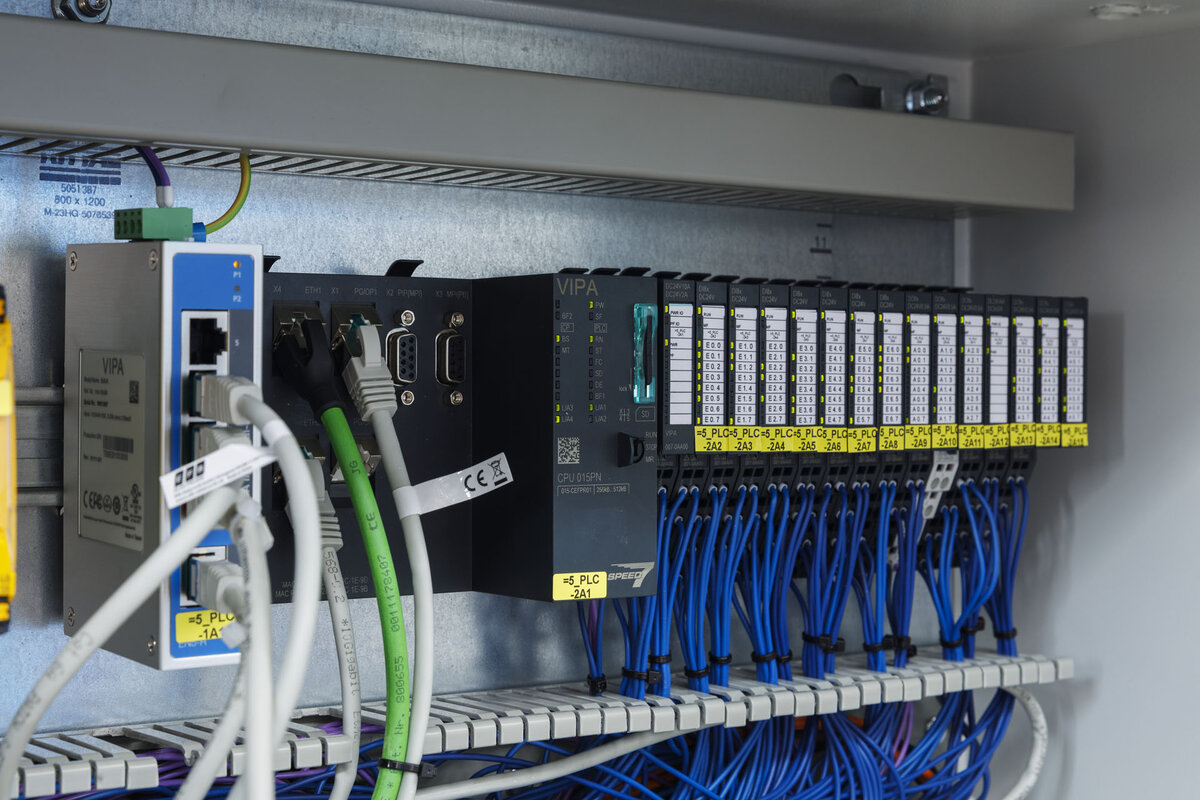
Motoman GP50 handling robot with Servofloat function
After positive experiences with Yaskawa in the past, Baumann Group managers decided to use a Yaskawa model for the handling robot, too, specifically a 6-axle Motoman GP50 with 50 kg load capacity. This positions the up to 15 cm thick paper stack before cutting and it also handles the removal of the paper from the machine after cutting.
As a special feature, the robot employs a so-called Servofloat function. This enables the control software to smooth out individual robot axes, so that the robot can effectively simulate the dexterity and touch of a human operator and react to smallest changes in force. One axis of the robot is set without power and tilted for the system. This ensures an accurate, smooth cut of the paper stack in the machine.
The compact Motoman robot controller YCR1000 in the control cabinet is integrated into the higher-level machine controller. This allows the robot to be controlled in the widely used IEC 61131 PLC environment. The integration into the PLC preserves all the genuine advantages of the robot control system.
As a solution provider, Yaskawa was able to offer robot and control technology from a single source, thus ensuring that all components are optimally matched to each other. Yaskawa implemented the required connectivity via appropriate software and bus interfaces. In addition, the manufacturer impressed with its delivery performance and a personal touch in customer interactions.
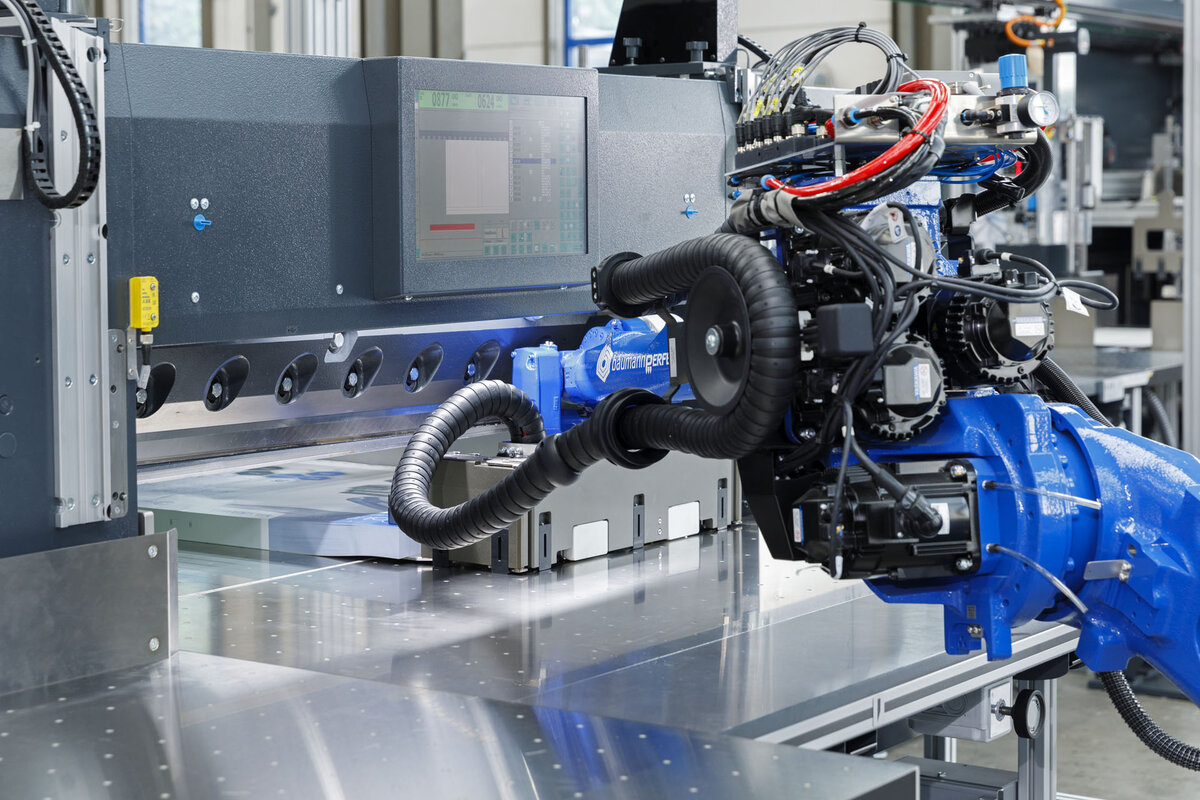
Summary
The fully automatic baumannperfecta jogging and cutting system revolutionizes paper processing in the graphics industry: No operator intervention is necessary between loading the pallet with the printed sheets and removing the finished products. Yaskawa robot and control technology ensures the necessary efficiency and precision in all aspects of the automated cutting process. “From our point of view, there were two main points in favor of this supplier,” summarizes Markus Frick, Managing Director of the Baumann Group: “Firstly, Yaskawa has decades of experience in mechanical engineering and especially in the printing industry. And secondly, we value the geographical proximity: Yaskawa's European headquarters in Hattersheim near Frankfurt is just an hour's drive away. This means that for training and support the distances are short.”