Più di 100 anni di progresso tecnico ci hanno resi leader nei settori degli Inverter, dei servoazionamenti, della tecnologia di controllo e della robotica.
Automazione altamente flessibile per la produzione su larga scala di componenti per e-bike
Investimento nella mobilità elettrica
Morat Swoboda Motion si è lanciata nell'era dell'elettromobilità con un progetto pionieristico di automazione. Il produttore di componenti di azionamento per applicazioni di elettromobilità - fondato a Nowa Ruda, in Polonia, nel 2018 - ha eretto un impianto di produzione su un nuovo terreno.
Morat Swoboda Motion è una joint venture tra il gruppo Franz Morat e il fornitore automobilistico Swoboda. Da oltre 100 anni, il gruppo Franz Morat è tra i migliori specialisti della tecnologia di azionamento e produce di tutto, dalle ruote dentate ai motori di azionamento completi. Con una forza lavoro di 4.200 persone, Swoboda sviluppa e produce componenti e sistemi innovativi ad alta precisione per il futuro dell'automobile.
Con la fondazione della joint venture, le due aziende hanno deciso di dirigere le proprie attività future verso la mobilità elettrica. Entrambe le aziende hanno acquisito esperienza nella produzione di componenti per unità di azionamento elettriche. "Il primo contratto congiunto per la fornitura di componenti di cambio per motori da e-bike non è stato solo il più grande nella storia del Gruppo Franz Morat, ma anche una grande sfida per un'azienda di medie dimensioni. Ecco perché la joint venture ha rappresentato la soluzione migliore per tutte le parti coinvolte", spiega il direttore generale del progetto Stefan Mayer.
Nello specifico, la sfida consisteva nella costruzione di un impianto di produzione, nella progettazione e allestimento delle linee e nel reclutamento di personale qualificato - il tutto in tempi stretti. Mayer ricorda: "C'è stato solo un intervallo di sei mesi tra l'ordine e la cerimonia di posa della prima pietra nel luglio 2018. Le macchine sono state consegnate a Nowa Ruda in novembre e i primi campioni hanno lasciato lo stabilimento nel marzo 2019".
Soluzione di automazione unica nel suo genere
La ricerca di una strategia di automazione adeguata per il collegamento intelligente e flessibile dell'intero parco macchine si è rivelata una sfida importante. Inoltre, poiché richiedeva il massimo grado di automazione possibile con il minimo dispiegamento di manodopera, è stato necessario trovare una soluzione di carico completamente automatica per ogni macchina.
Le idee inizialmente discusse consistevano in una serie di soluzioni di diversi produttori, ma queste non sono riuscite a soddisfare pienamente le aspettative. Tuttavia, la presentazione di un progetto completo da parte di EGS Automatisierungstechnik di Donaueschingen ha permesso di identificare la soluzione finale. "In effetti, siamo stati sorpresi di scoprire che il nostro compito complesso poteva essere risolto utilizzando componenti modulari EGS standard", afferma Mayer.
Ingegnoso sistema di automazione e interconnessione
Hartmut Pfalzgraf – appartenente al team di vendita EGS- ha riconosciuto immediatamente che tutti i requisiti potevano essere soddisfatti in modo ottimale con il sistema di pallettizzazione SUMO Ecoplex2: "Il nostro innovativo sistema universale ha due carrelli per lo stoccaggio dei pezzi e un robot Yaskawa MOTOMAN per la movimentazione dei pezzi, compreso il carico e lo scarico della macchina. Questo ci consente di automatizzare e collegare simultaneamente le macchine: in questo modo il processo risulta altamente flessibile grazie al trasporto manuale dei carrelli".
La soluzione chiave per una semplice concatenazione di macchinari in Morat Swoboda Motion sta nell'uso di un sistema uniforme di pallet che possono essere adattati alla specifica dimensione del pezzo mediante supporti e distanziatori a seconda del componente. Una volta che tutti i portapezzi di un carrello sono stati riempiti con le parti lavorate, un addetto rimuove il carrello, lo spinge alla stazione di lavorazione successiva e lo dispone per l'ulteriore lavorazione. Le parti finite di una stazione sono le grezze della successiva.
“Questo sistema è semplice ma ingegnoso. Le nostre ruote e i nostri alberi passano attraverso l'intero processo di produzione senza ricorrere ad interventi manuali di riordino o lavorazione. Il trasporto manuale con carrelli è invece il modo più semplice e sicuro per trasferire le parti da A a B, ed è impareggiabile in termini di flessibilità ", afferma Mayer.
Questo concetto di produzione altamente flessibile offre un ulteriore vantaggio decisivo. In caso di guasto di una delle macchine o dei robot, la linea non si arresta completamente, come nel caso di un collegamento rigido degli elementi di produzione. La produzione può continuare in via ridotta.
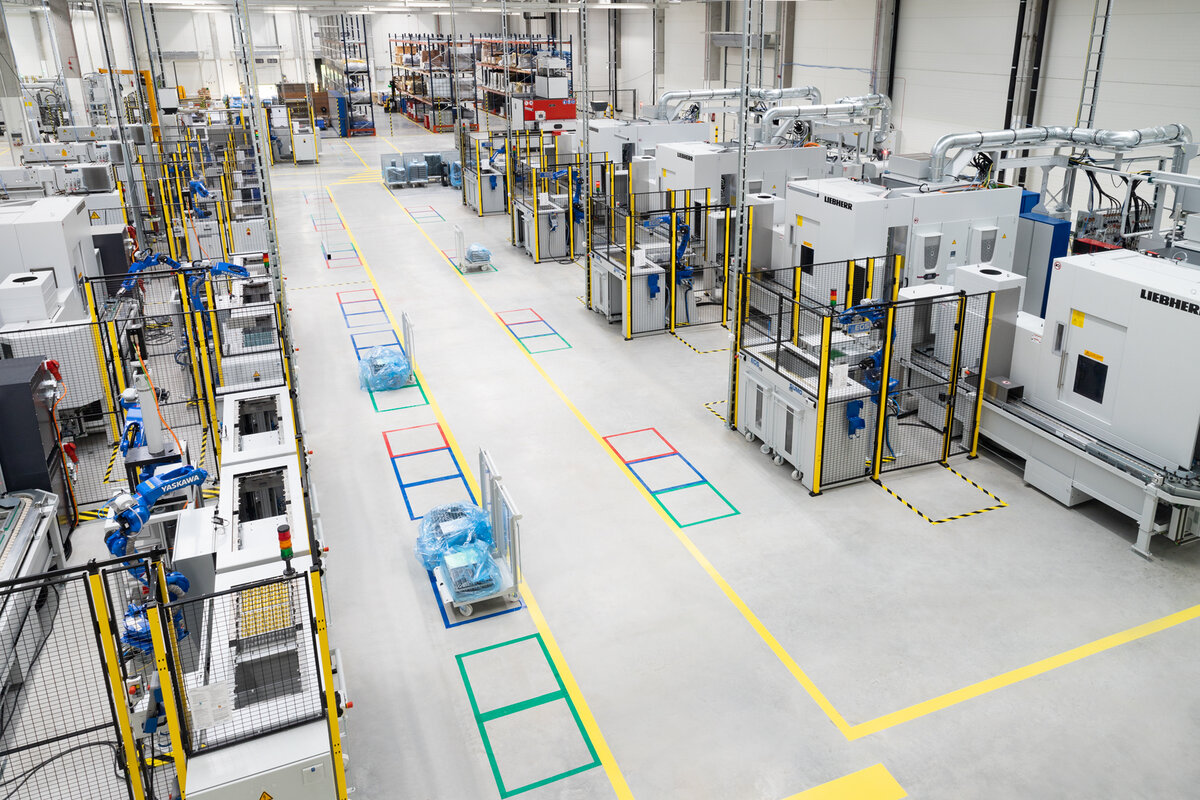
Controllo dell'automazione delle macchine
Ogni centro di lavoro ha almeno un sistema Ecoplex2 e un robot Yaskawa. Qui EGS utilizza un solo tipo di robot: il collaudato Yaskawa MH12. Dotato di sei assi, è la soluzione ideale per il caricamento della macchina: è veloce, preciso, incredibilmente affidabile e ha un'ampia portata. Pfalzgraf commenta: “Il range di 1.440 millimetri dell'MH12 ci consente di posizionare il robot alla giusta distanza dalla macchina utensile, con il conseguente vantaggio di avere libero accesso ad essa. L'operatore può eseguire le misure di servizio o, se necessario, il caricamento manuale senza ostacoli".
Solo in un singolo caso EGS ha dovuto modificare la scelta del tipo di robot, quando complesse attività di carico e scarico di una macchina in accordo a rigorosi criteri di tempo di ciclo hanno richiesto due robot a sei assi. Questo compito particolarmente complesso è condiviso da un MH12 e un MH5 LSII, piccolo e compatto.
“In Framo Morat già utilizzavamo robot Yaskawa e la nostra esperienza è sempre stata delle migliori. Poiché solo i robot più affidabili erano adeguati all'impianto di Nowa Ruda, abbiamo deciso di puntare sul sicuro, con Yaskawa", afferma Mayer.
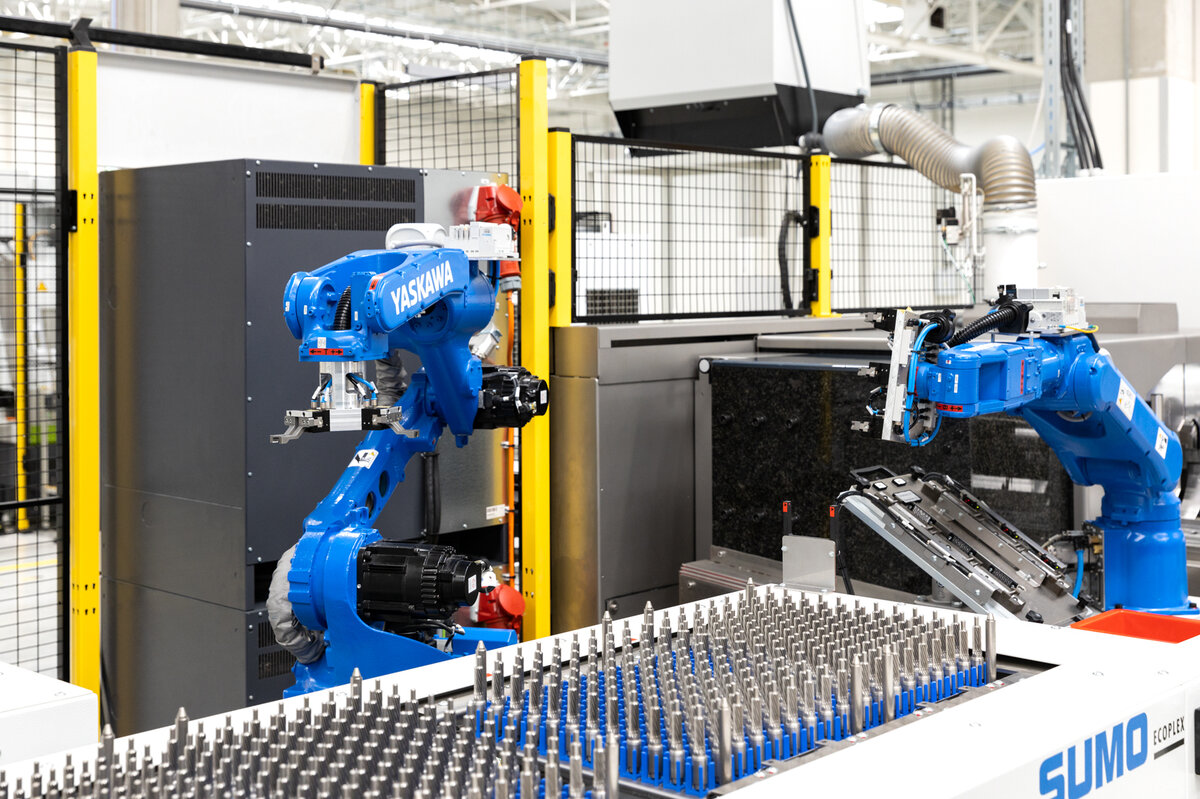
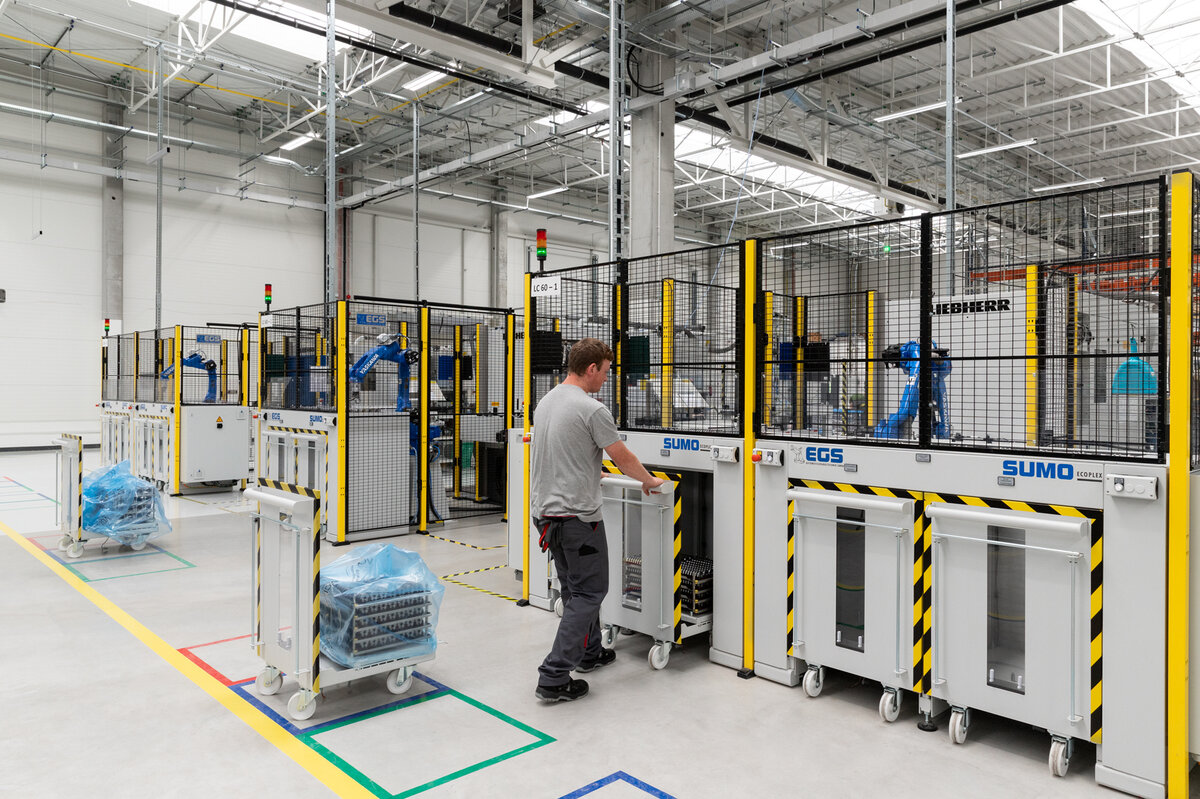
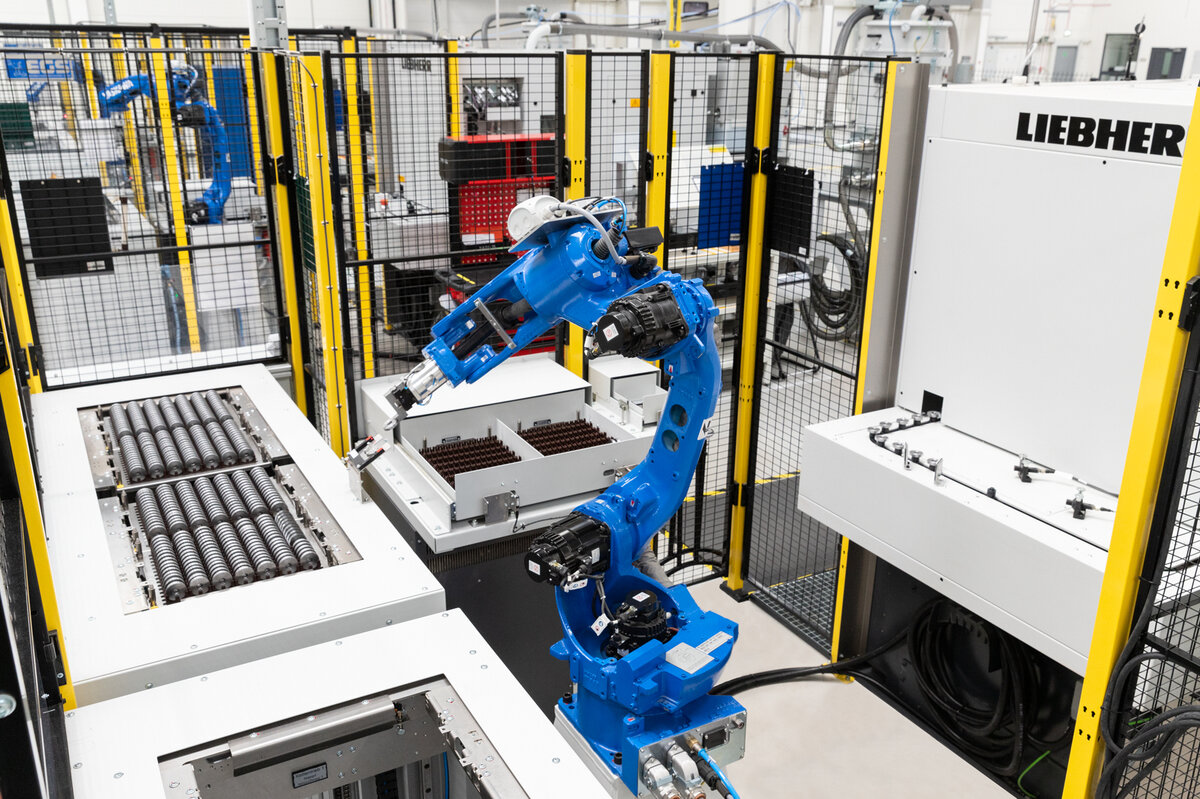
Produzione lean nel vero senso della parola
L'alto grado di automazione e la configurazione intuitiva dell'intero sistema ha sicuramente dato i suoi frutti nella linea di produzione con 16 robot Yaskawa e 20 sistemi SUMO Ecoplex 2. Il centro di lavoro e il robot comunicano tramite il controller Yaskawa DX200.
La qualità è un tema centrale in Nowa Ruda. Sebbene il parco macchine e i robot combinatiu con un grado di automazione estremamente elevato raggiungano i vertici della precisione di ripetizione, vengono comunque regolarmente eseguiti test di verifica.
Il project manager Mayer guarda al futuro di Nowa Ruda con un misto di orgoglio e sollievo: “L'avvio della produzione ha avuto molto successo. Tutti i componenti hanno soddisfatto le nostre aspettative. E se dovesse esserci un forte aumento, come previsto, nella domanda di componenti per e-bike, potremmo semplicemente estendere la nostra produzione modulare altamente flessibile”, afferma Mayer.