Più di 100 anni di progresso tecnico ci hanno resi leader nei settori degli Inverter, dei servoazionamenti, della tecnologia di controllo e della robotica.
Highly automated production of several million connectors
- Industrie
- Chimica / Plastica
- Automotive
- Applicazioni
- Dispensing | Sealing
- Client
- EGS Automatisierungstechnik
- KE Elektronik
Intelligently linked and consistently automated
How to cope with the constantly increasing demand for plastic hybrid components in spite of space and personnel constraints? An international automotive supplier has opted for an intelligently linked system with two injection moulding machines and six robots – and is faring very well.
With around 3,000 employees worldwide, KE Elektronik is one of the most valued suppliers to the automotive and aviation industries. With production sites in Germany, the Czech Republic, Slovakia, northern Macedonia, China and Mexico, the company belongs to the American Amphenol Corporation – a leading manufacturer of connectors.
For some time now, the products manufactured by the 300-strong company at its headquarters in Kressberg-Marktlustenau have included engine fan connectors that are used in both hybrid vehicles as well as those powered purely by internal combustion engine. These connectors are so-called plastic hybrid components in which four metal contacts are overmoulded with three different plastics.
“The production of these connectors is a relatively complex process that involves numerous testing stages as well as complete traceability. In order to be able to meet the constantly increasing demand given the shortage of skilled workers, an intelligent automation solution was required,” says Jens Gradenegger, Team Leader Injection Moulding Automation at KE Elektronik.
An extremely challenging project
KE Elektronik turned to EGS Automation GmbH in Donaueschingen to take on the task of automating and interlinking two punching and bending units and two Arburg injection moulding machines in such a way that the resulting manufacturing island could achieve an output of several million connectors per year. “Our previous experience of working with EGS was positive, so we were sure they’d be able to offer us a reliable solution in this case as well,” says Jens Gradenegger.
EGS would not be EGS if it wasn’t able to come with a perfect automation solution to do this complex job. “We like to prove our expertise by taking on challenging projects – and this one certainly gave us plenty of opportunity to do so. In close cooperation with KE, we succeeded in designing a 15 x 6-metre manufacturing island that meets all requirements, including six Motoman robots by Yaskawa, lots of handling and testing technology and a SUMO Ecoplex2 palletising system,” says EGS project manager Hartmut Pfalzgraf.
The complete line is clearly divided into four modules – and the clarity of the layout is impressive. In order to guarantee the cycle time specifications of less than ten seconds per connector as well as maximum availability, only the highest quality components are used. Attention was also paid to good accessibility in all parts of the system. And this is what the system looks like in practice:
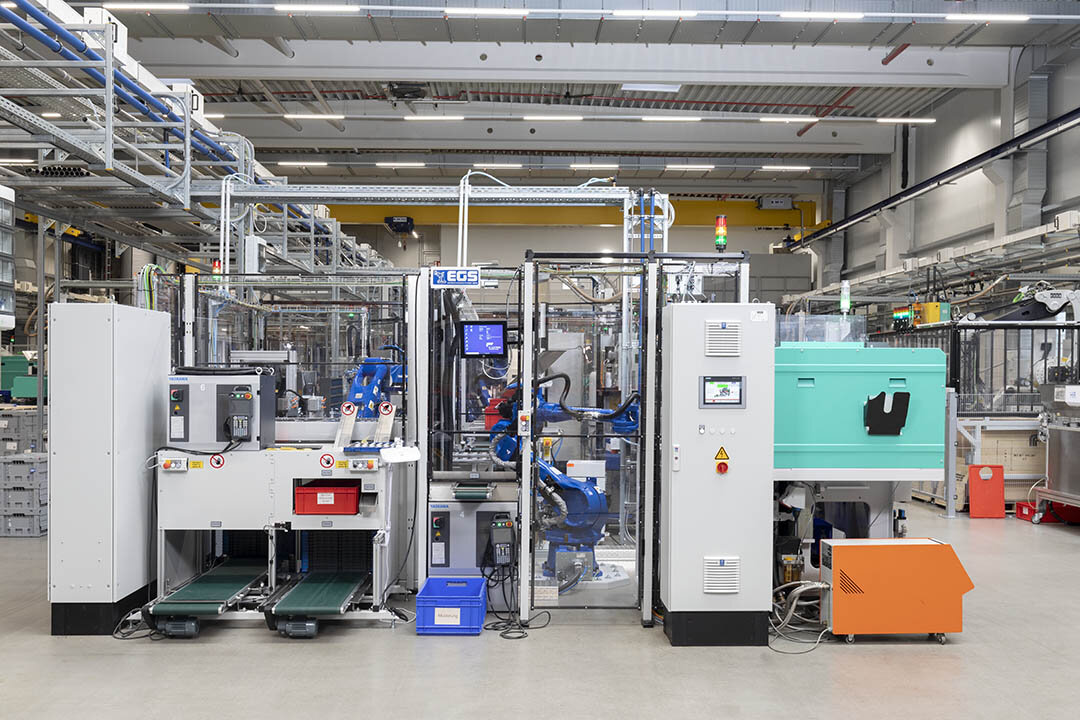
Module I: Provision of the connector pins
Two punch-bend units ensure continuous provision of the connector contacts. While one line produces signal pins, the other produces power pins. A MOTOMAN GP7 with mechanical gripper – equipped with integrated sensor technology and tilted by 25 degrees – is installed on each punch-bend unit. “The inclined position of the robot allowed us to realise the required rotation from the removal position to the insertion position entirely via the S-axis, thereby reducing the cycle time to a minimum,” says Hartmut Pfalzgraf – an ingenious piece of engineering that reflects EGS’ experience of over 2,000 robot installations.
The two 6-axis robots each remove two contacts from their line and position them in a workpiece carrier with four receptacles, each of which in turn has to be fitted with four contacts. After four work cycles, the two 6-axis robots have completely loaded the four receptacles and the workpiece carriers reach their unloading position, where they are received by the MOTOMAN GP50 on Module II.
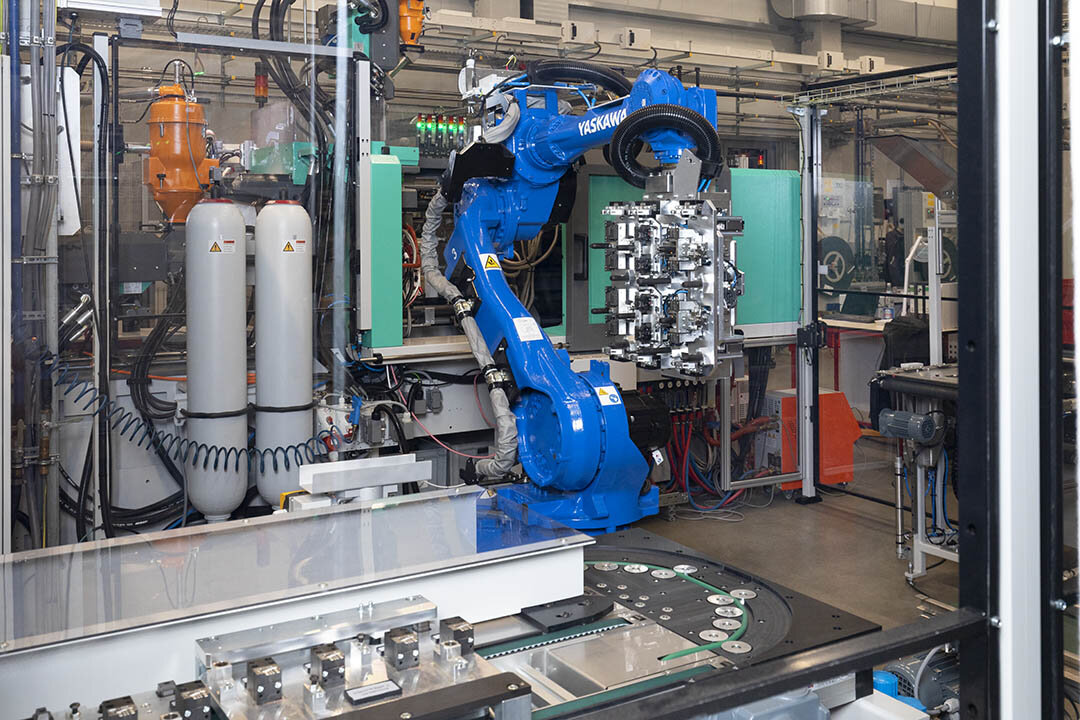
Module II: Complex handling processes with the GP50
The heart of Module II is a 2K injection moulding machine by Arburg on which two plastics are processed simultaneously. In the first shot, an overmould is applied with the upper mould of the SGM to fix the contacts precisely in the desired position. The resulting contact carriers are then overmoulded to a connector plug in the second shot by means of the lower injection mould.
All loading and unloading processes of this SGM are taken care of by a Yaskawa MOTOMAN GP50 6-axis robot, on which a 36 kg triple gripper system is mounted. With a reach of 2,061 millimetres and a payload of 50 kg, the robot is perfectly suited to this task. The task spectrum of the 6-axis robot is highly complex.
The robot first has to unload the SGM before it can fit it with new contacts. To do this, the 6-axis robot must remove the finished overmoulded connector plugs from the lower mould, transfer the pre-moulded parts from the upper mould to the lower mould and finally fit the now empty upper mould with the 4x4 stamped and bent contacts from the workpiece carrier of Module 1.
“In order to be able to achieve the required precision when gripping, the robot docks onto the moulds by means of a centring gripper prior to the actual handling. To keep the mould open time as short as possible nonetheless, we make full use of GP50’s the exemplary dynamics,” says Jens Gradenegger.
Finally, the overmoulded connectors are placed on another workpiece carrier on the programme. With a total of eight connectors, the workpiece carrier is transferred from Module II to Module III via a transfer system.
Module III: Special LSR overmoulding
The essential process step in Module III consists of LSR overmoulding of the connectors, which is also carried out on an Arburg injection moulding machine. The advantage here is that by overmoulding the connectors with a silicone lip, a separate seal is not required so there is no need for an additional component that might cause problems during assembly.
Module III also uses a MOTOMAN GP50, but its work is not quite as complex as that of its colleague in Module II. Here the robot removes the 2x4 connectors from the workpiece carrier and checks their temperature by holding them in front a thermal imaging camera. Only when the temperature is within the defined window are the parts suitable for the next injection moulding process and the robot then places them in the mould.
Here, too, the first step before loading the injection moulding machine is to remove the eight finished parts. The GP50 then loads a 2-fold shuttle which takes a total of 16 parts to the last module.
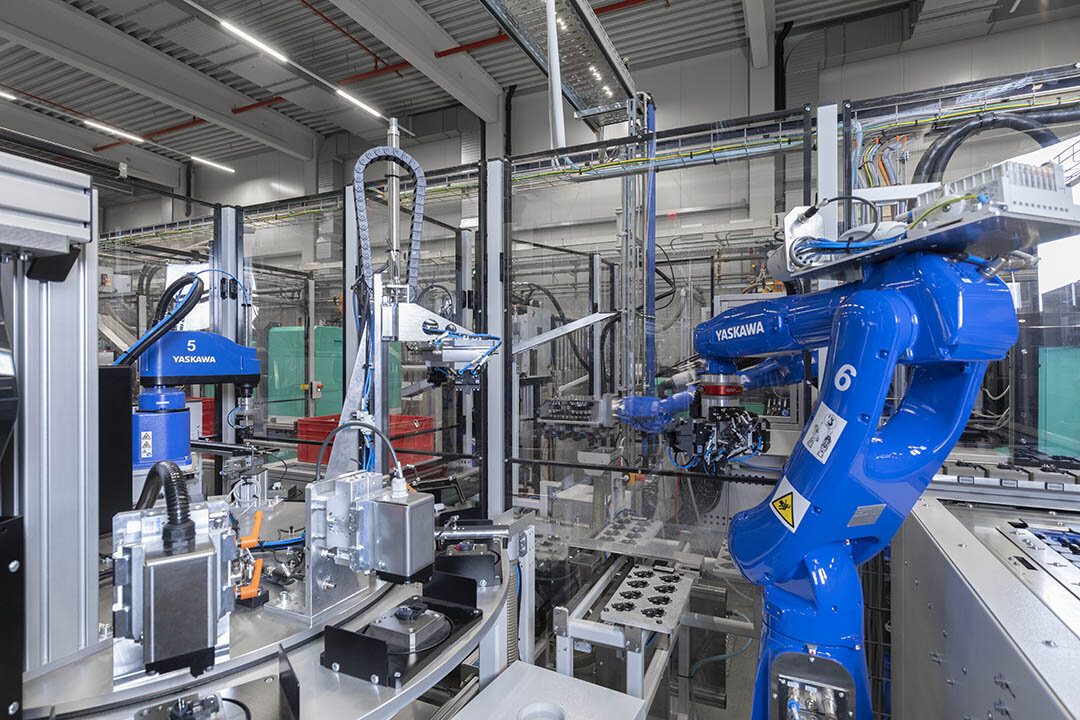
Module IV: Test, test, test
Another MOTOMAN GP7 is used on Module IV, where the task is to pick up the finished parts and move them to a revolving transfer unit. “On this revolving transfer unit there are various test stations and an assembly station equipped with a MOTOMAN SG650 Scara robot. Here we’ve succeeded in integrating a really large number of processes in an extremely compact space,” says Jens Gradenegger.
This module is in fact is all about quality assurance. The first step is a continuity and high-voltage test, followed by a pin position check with a triangulation laser, and then a camera inspection of the LSR overmoulding, before the component is given a data matrix code by a marking laser, thereby ensuring one hundred percent traceability. Subsequently, the DMC is tested, too.
Once the component has passed the entire test marathon as a good part, the final step is the torque-controlled assembly of a protective cap, which is performed by the SG 650 Scara robot. “The fact that Yaskawa has now been offering 4-axis robots for some time has proven to be a great advantage here. This allowed us to fit the entire plant with robots made by a single manufacturer and stay with Yaskawa on the control side,” says Jens Gradenegger.
The Scara robot is not pushed to its limits, but the situation is different with the MOTOMAN GP7: “The 6-axis robot is critical in terms of the time cycle because it not only loads the rotating transfer unit but also finalises the process by placing the finished parts in trays in a SUMO Ecoplex2 – the top seller among the EGS palletising systems. We had to pull out all the stops here so as not to jeopardise our cycle time targets. Among other things, the robot is fitted with a 2+2 gripper system to reduce the number of movements,” says Hartmut Pfalzgraf.
The plant has been running in three shifts since September 2021 and fully meets KE’s expectations, as Jens Gradenegger assures us: “EGS really did an excellent job – from planning right through to commissioning. We were able to benefit from the expertise of the EGS designers in all kinds of detailed solutions. Added to this is the customary reliability of Yaskawa robots, which we particularly value here at KE.”
Text: Ralf Högel
Contact for readers’ inquiries:
Tel. +49-8166-90-0
Fax +49-8166-90-103