Più di 100 anni di progresso tecnico ci hanno resi leader nei settori degli Inverter, dei servoazionamenti, della tecnologia di controllo e della robotica.
Ixapack Global packing and packaging
French automated packing and packaging machine manufacturer iXAPACK GLOBAL opts for Yaskawa Sigma-7 servo system
- Industrie
- Chimica / Plastica
- Alimentare
- Agricoltura
- Applicazioni
- Picking | Packing
- Client
- iXAPACK Global S.A.S.
Challenge
Compact precision
For its new product line, experienced packing and packaging machine manufacturer iXAPACK GLOBAL was on the search for a compact, yet high-precision servodrive package. It found the perfect solution in the current dual-axis modules of the Sigma-7 servo system series from Yaskawa. Combined with the compact MP3300 controller, the Sigma-7 range delivers the highest standards in high-speed performance and accuracy within the smallest space.
Solution
40 years of history
Over its forty-year history, iXAPACK GLOBAL, headquartered in Mauléon, western France, has become a specialist in the design and manufacture of automated packing and packaging machines. The company's portfolio comprises three separate brands, iXAPACK PACKAGING, SELVEX, and AUCOUTURIER, ranging from complete packaging lines for the most varied applications to inspection systems. iXAPACK pursues the highest standards in quality and innovation. This is true both of its own development and production operations in France and of the components it sources from suppliers.
iXAPACK GLOBAL recently developed two new products to automate the cartoning process. These developments consist of delta robots and multi-articulated manipulators to combine product gripping and carton folding operations. Up to five robots can be controlled by one controller, which synchronizes the movements of the different robots as well as the feed systems.
In view of this, the servo drives require the highest speed and precision. There are also 108 or 74 servo axes installed in the respective machines. iXAPACK GLOBAL was, therefore, looking for a high-performance and, above all, compact servo drive solution that would take up minimal space in the switching cabinet.
In the end, the company opted for the Sigma-7W dual-axis modules from Yaskawa. Controlling two motors with a single amplifier reduces the amount of space taken up in the switching cabinet and machine even further, and saves energy.
Result
The Sigma-7 servo system series
The Sigma-7W dual-axis modules are available in both 200 V and 400 V versions. iXAPACK is implementing both versions. Their external appearance is almost identical to the single-axis amplifiers, meaning in particular that they have a space-efficient, book-style enclosure, which is only 80 mm wide. This equates to a width of only 40 mm per axis for the dual-axis module. In addition, a holding brake can be directly attached to the amplifier, rendering other components superfluous and following the trend of increasingly compact solutions.
A further benefit of the Sigma-7W modules is that both axes can be coupled using the internal DC bus. In certain configurations, such as during simultaneous generator and motor operation, the coupled axes require much less energy than two single-axis modules, offering potential energy savings of up to 20 percent, depending on the configuration. The dual-axis module can also be completely supplied by the DC bus through a DC input. Naturally, both axes of the Sigma-7 series dual-axis module meet the high safety requirements of the SIL3 standard for STO (Safe Torque Off).
Development of the new Sigma-7 servo drive series focused on three main goals: efficient commissioning, high production output, and maximum operational reliability. Through this series, Yaskawa offers a powerful response to today's market requirements for both machine constructors and final customers in the production industry.
Extensive presets in the amplifier software simplify and accelerate the servo drives' commissioning. For example, the 'tuning-less' function allows immediate use of the Sigma-7 without the need for complex parameterization or special knowledge of control equipment, while an autotuning function ensures quick adjustment. By saving time, you also benefit from savings in costs.
The servo motor system supports both installation and commissioning on the hardware side too. The new 400 V version has a removable quick-coupling plug, made according to European standards, for easy and simple cable wiring. Moreover, the book-style enclosure supports gap-free, side-by-side installation of several amplifiers in a small space. This makes it possible to realize a high-performance density inside the switching cabinet. The space inside the cabinet is reduced to a minimum, allowing it and the drive electronics to be integrated in the machine.
Devices can also be connected directly from one to the next, so-called daisy-chain wiring, which reduces installation time. An integrated real-time EtherCAT interface is also available for easy integration in the machine environment. Taken together, all of these time-saving features considerably reduce the time to market of the machine.
The motors in the Sigma-7 series are up to 20 percent smaller than their predecessors while offering equivalent performance, and they produce considerably less heat. This means that they not only need less space in the machine but they are also more energy-efficient. Much more potential for efficiency is provided by the software and electronics. Sigma-7 is characterized by its particularly powerful control algorithms.
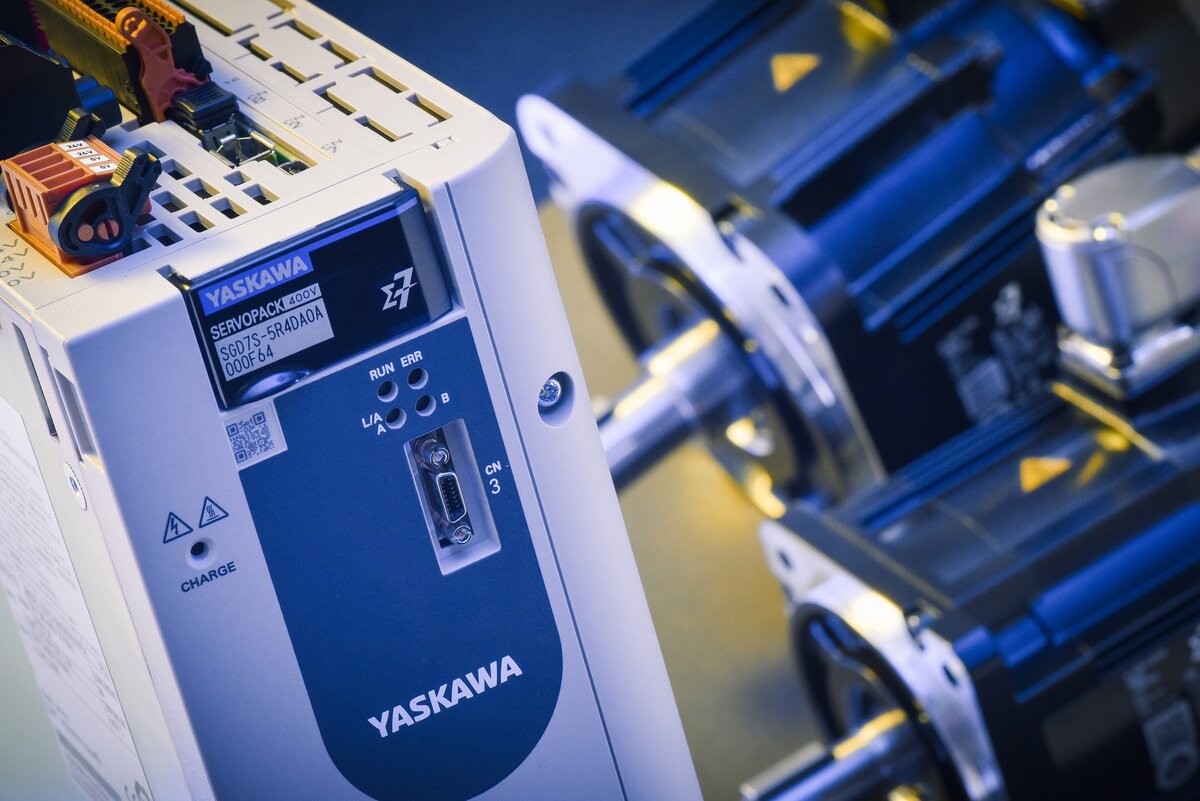
Compact MP3300 and MP3300iec controllers
The extremely compact MP3300 and MP3300iec controllers from Yaskawa offer unrivaled standards in high-speed performance and accuracy. Alongside the standard MP3300 version, the MP3300iec variant has been designed specifically with the European market in mind. Its IEC development interface ensures simple, fast, and user-friendly programming in accordance with the IEC 61131-3 standard.
Both MP3300 models feature a powerful CPU, making possible a high-speed scanning cycle of at least 125 microseconds or 64-bit data types for example. As a result, greater precision can be achieved in complex high-speed applications. Simple usability and easy maintenance were also focal points during development.
Featuring real-time MECHATROLINK III Ethernet interfaces, the new compact controllers enable simple integration of servo axes in synchronous groups. The CPU size and base unit can be selected freely, meaning that, in the event of future expansion, the performance can be increased by adding a larger CPU. Two base units are available for input and output modules – with either one slot or three slots depending on application.
The MP3000 series was developed specifically for highly complex systems with many axes. The components in the series deliver a high level of performance, as required, for example, by machines for semiconductor coatings. They are at least 1.5 times more powerful than their predecessors. Thanks to the built-in technology of the Sigma-7 servo systems, including machine vibration absorption and power ripple compensation, the MP3000 controllers are able to increase productivity significantly by reducing cycle times.
Controller performance was a particular focus in development of the MP3000 series. Power can be evenly distributed between the axis control and PLC functionality. This ensures that sufficient computing power is available for PLC functions even during highly complex curve movements and high cycle rates that require a great deal of processing power for the motion control component.
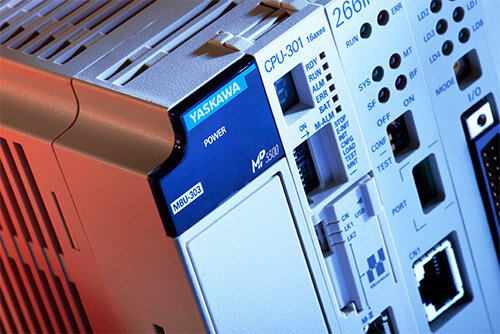