Più di 100 anni di progresso tecnico ci hanno resi leader nei settori degli Inverter, dei servoazionamenti, della tecnologia di controllo e della robotica.
PL80 and PalletSolver software automate WILLIAMS & HUMBERT winery
Yaskawa's solution with a PL80 robot and PalletSolver software allows Proelan to automate and make production at WILLIAMS & HUMBERT Winery more flexible.
Proelan is a company with more than sixty years of experience in the industrial engineering sector. The company, based in Seville, Andalusia (Spain), has made available to the market innovative and diversified technological solutions in the different industrial branches, through a highly specialized team.
In recent years, it has incorporated a newly created department to promote the development of projects with a high degree of robotization and has created one of the largest robotics training classrooms in Spain. Since then, always relying on the leading brands in the market, it has become one of the leading companies in the development of automation projects with robotics integration in a wide variety of sectors.
- Industrie
- Beverages
- Applicazioni
- Palletizing
Automation of the WILLIAMS & HUMBERT winery for a production of more than 5,000 bottles per hour
Involved in the creation of the “Appellation of Origin”: Jerez-Xérès-Sherry, the WILLIAMS & HUMBERT winery is recognised as one of the most prestigious producers in the world. A reputation that must be backed up by the production of wines of the highest quality, but which must also respond to the needs of an increasingly globalised market.
As a result of its success, the WILLIAMS & HUMBERT winery wanted to undertake an automation project that would allow it to significantly increase its production. To this end, the company from Jerez relied on the experience and know-how of Proelan for the design, installation, and commissioning of a new system for packaging up to 5,000 bottles per hour.
Due to the intrinsic characteristics of a winery, the Proelan team quickly realised that this was a special project. With very little space available, they needed to realise a solution that would pack all the cases coming in from up to two different lines. In addition, they needed to complete it in a record time of just 3 months.
In addition to these time and space requirements, there was an even more difficult challenge to meet: the more than 40 different crate variants that had to be processed by the system. WILLIAMS & HUMBERT was looking for a differentiating solution on the market, a system flexible enough to create any format for palletizing and to do so in a simple manner.
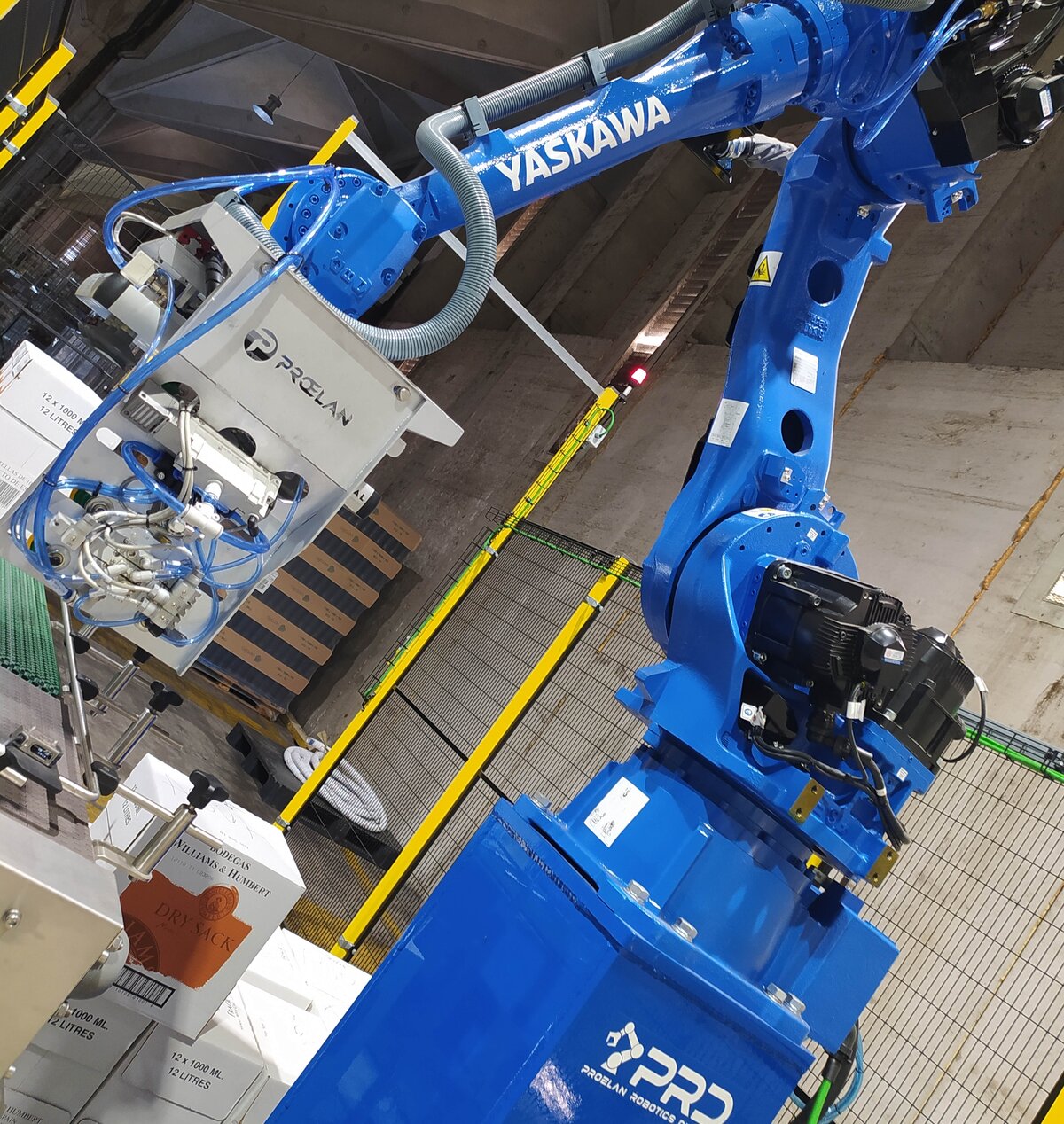
A single PL80 robot to handle palletizing on two production lines
For all these reasons, the PL80 palletizing robot from Yaskawa was the ideal solution. With dozens of projects behind them relying on the Japanese manufacturer's robotization solutions, Proelan, Yaskawa's partner, decided on a product that they knew perfectly well and that fitted the needs of WILLIAMS & HUMBERT Winery like a glove.
Thanks to the PL80 robot's large work envelope and high working speed, as well as the flexibility provided by the PalletSolver software, an efficient and even elegant solution was designed, capable of handling the two lines in a unique way.
However, in a project with such tight deadlines as this one, it is essential for the engineering companies that the manufacturers provide them with as much data as possible, and that they do so in a reliable manner. The large amount of information that Yaskawa puts in the hands of the engineers, as well as its total availability to answer any questions they may have, was a key factor in Proelan's confidence, once again, in a Yaskawa solution.
After visiting the facility and gathering all the information, they returned to their robotics classroom. This workshop with 2,000 m2 of facilities for engineering, machining, etc. allows Proelan to offer a holistic service. A service that proved fundamental in this project, as it required the design of a fully customised gripper to manage the huge variety of boxes, which not only included different sizes and shapes, but also some in open format that increased the complexity of the system.
This gripper, made possible thanks to a classroom at the technological forefront of the sector and a highly specialized team with a long track record, was designed and created entirely from scratch by the Proelan team. A large number of analyses and tests were carried out, resulting in a versatile, flexible and lightweight solution; fundamental characteristics both for the management of current formats and for future updates.
In this same space, and thanks to Yaskawa's simulator, MotoSim, the complete equipment was virtualised, being able to observe the mechanical interferences, correct them and adjust the robot to carry out its work in the best possible way.
A work that, thanks to the functionality of MotoSim, does not stop at the design phase. The application allows all the physical drawings and configuration data obtained during the design phase to be directly transferred to the robot. A possibility that greatly speeds up times and reduces programming costs.
Finally, thanks to a sales and distribution network that has been well-oiled for more than 30 years in the Iberian Peninsula, Yaskawa Ibérica has even reduced the delivery time from the initial eight weeks to just two.
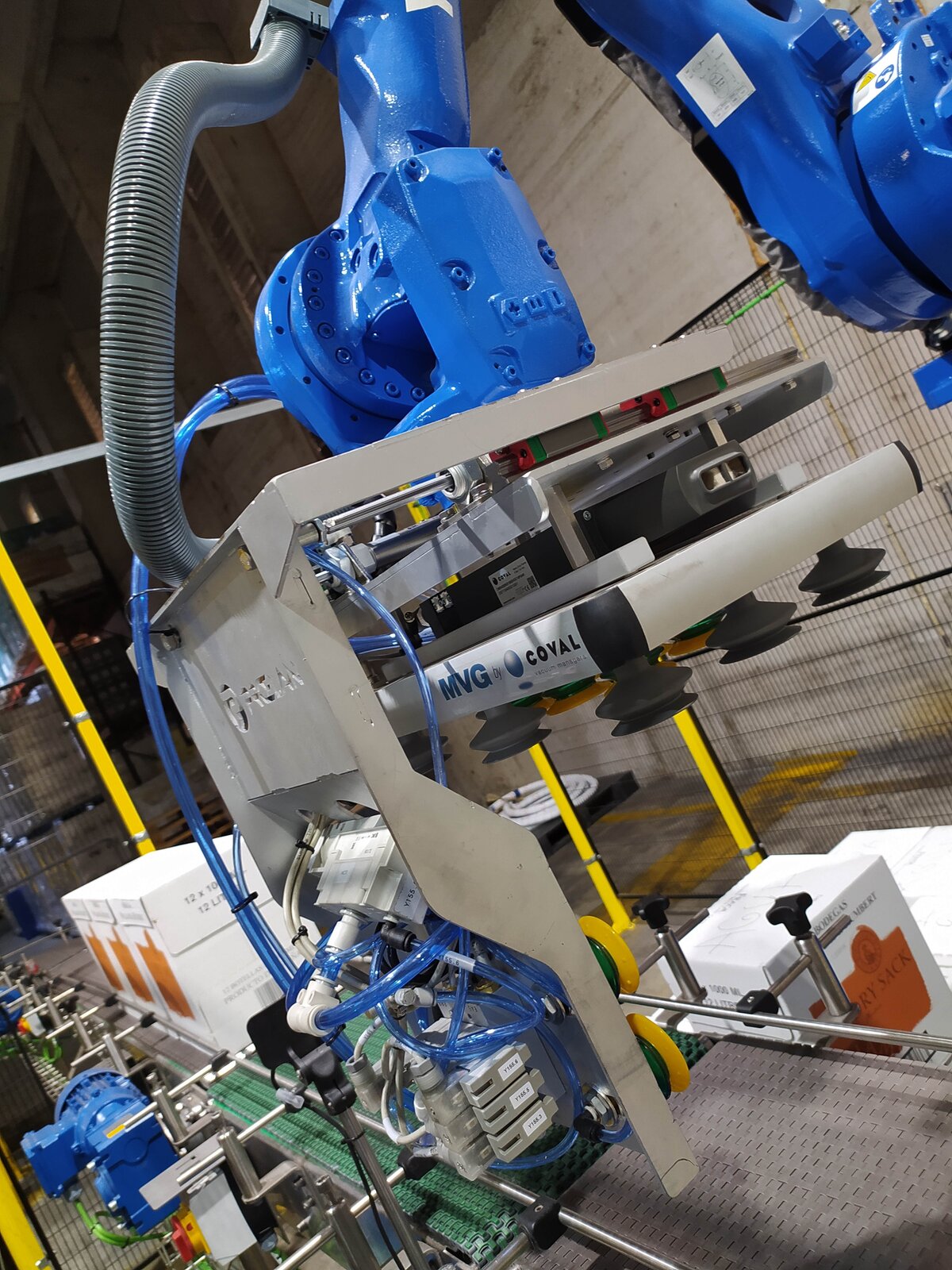
Flexible and adjustable case palletizing thanks to Yaskawa's PalletSolver software
Thanks to its kinematics, the small palletizing and handling robot, the PL80 palletizing robot was the ideal solution for palletizing crates at a very high rate and in a reduced space required by WILLIAMS & HUMBERT Winery. Especially if, as Proelan did, it is accompanied by Yaskawa's own PalletSolver software.
If the client was looking for a differentiating solution, in PalletSolver the engineering company found everything they needed. Despite not having worked with it previously, Yaskawa Ibérica accompanied them during a training process that, thanks to the simplicity of the program, took much less time than expected and will be of great help in future projects.
Its intuitive design and easy operation are the epitome of flexibility. With a modular design that pays special attention to customisation to suit each palletizing system, PalletSolver is configured in a series of simple steps. The software provides a series of screens for each infeed station, building and dispenser to enter the relevant data. In this way, only one user frame needs to be taught for each station and, during the run, the palletizing software automatically generates all the movement points for each cycle of the build.
Unlike other much more cumbersome solutions that require complicated programming processes, once the Proelan work has been completed, WILLIAMS & HUMBERT's own employees can adjust the robot's operation to suit the company's future needs.
In short, PalletSolver is a feature-packed software package designed for consistent palletizing and to enable rapid development and integration of the robotic palletizing system through user-friendly configuration and customisation. But also, to facilitate system uptime without compromising production performance, through a highly intuitive interface.
Initial forecasts exceeded with a fast, simple, and safe solution
One of the biggest concerns for companies that incorporate a robotics solution into their facilities is the safety of their employees. In this case, thanks to the FSU that comes as standard with Yaskawa robots, Proelan was able to define a robot workspace that will never be overtaken by the robot at any time.
The result is a fast, efficient, and simple solution, at the technological forefront of the sector, which, beyond meeting the initial requirements of 5,000 bottles processed per hour, has exceeded them in its few months of operation.
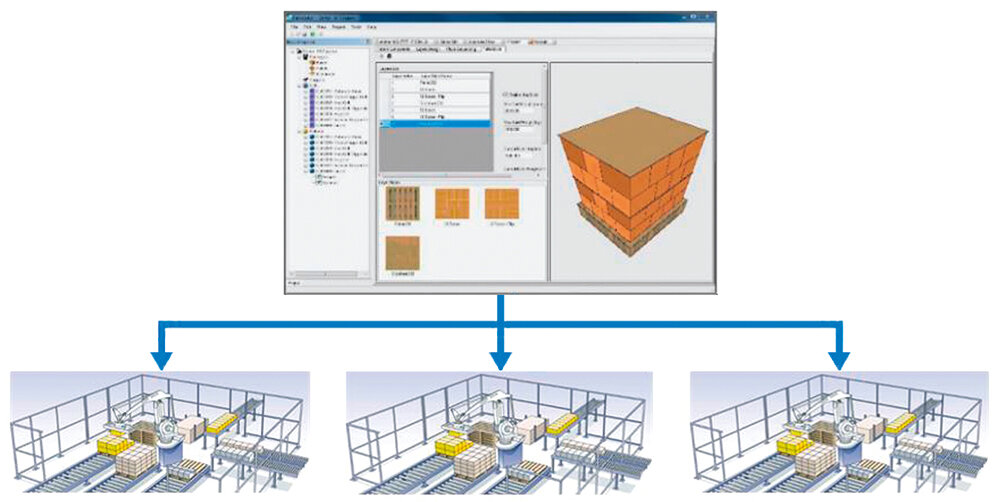