Più di 100 anni di progresso tecnico ci hanno resi leader nei settori degli Inverter, dei servoazionamenti, della tecnologia di controllo e della robotica.
Saldatura, collaudo, manipolazione perfetti
Binder e Yaskawa stabiliscono un nuovo standard in efficienza e precisione
Tutto doveva procedere rapidamente presso la Swabian Gebr. Binder GmbH Metallwarenfabrik. Un ordine su larga scala per la produzione di circa mezzo milione di parti in lamiera all'anno richiedeva una soluzione di produzione di classe extra. Insieme a Yaskawa, l'azienda si è prefissata di creare una cella di produzione che avrebbe stabilito nuovi standard in termini di output, precisione e disponibilità.
- Industrie
- Metallo
- Applicazioni
- Material Handling
- Saldatura a punti
- Quality Inspection
- Client
- Gebr. Binder GmbH
Con sede a Neenstette, il fornitore automobilistico svevo Binder – a conduzione familiare - gode di un'eccellente reputazione nel settore, grazie alla sua affidabile, orientamento al cliente e innovazione. Con i suoi circa 800 dipendenti, si focalizza sulla tecnologia di formatura e lavorazione della lamiera. Recentemente l’azienda è stata contattata da un importante costruttore automobilistico tedesco con un ordine per la produzione in serie di una struttura in lamiera per alloggiare le batterie a bordo di determinate serie di veicoli.
Thomas Pflüger, ingegnere meccanico e responsabile del reparto di tecnologia di giunzione e saldatura sostiene: "Gestire un ordine di tale portata - la capacità produttiva massima è di circa mezzo milione di battery frame all'anno - non sarebbe evidentemente possibile senza l'investimento in un sistema completamente nuovo, altamente automatizzato che integri i processi necessari di saldatura a punti, collaudo, e manipolazione".
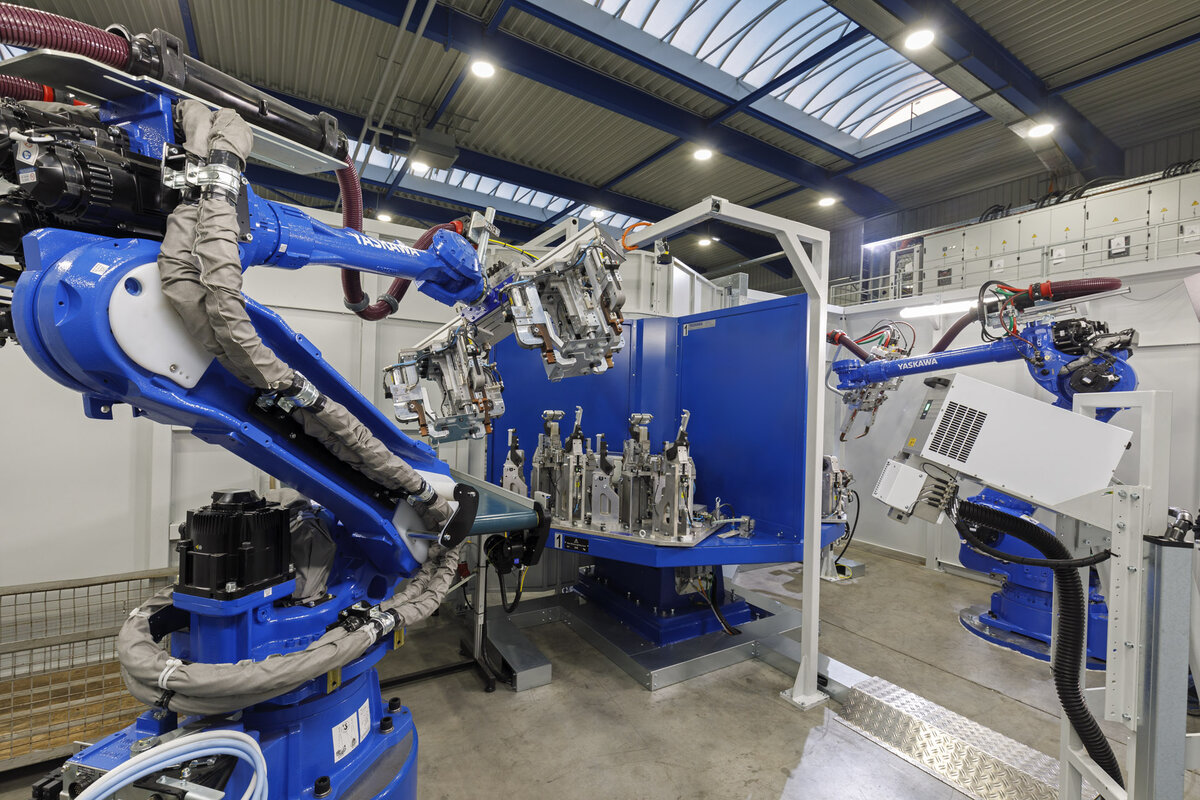
Un operatore, due robot, tre stazioni
Gli ingegneri di Binder hanno immediatamente iniziato a lavorare su una prima bozza, che ha delineato concettualmente le stazioni essenziali della nuova cellula robotizzata.
Roland Hermann, Senior Key Account Manager di Yaskawa, ricorda: "Tutti sapevamo che avremmo potuto raggiungere le specifiche del tempo di ciclo per questa parte di produzione di massa solo con l'uso di due robot a sei assi, uno per la saldatura a punti e l'altro per la movimentazione generale. Inoltre, una soluzione a tre stazioni prometteva di essere la più fattibile, consentendo l'implementazione di tutti i processi in parallelo e quindi indipendentemente dal tempo di ciclo. Mentre l'inserimento nella prima stazione è manuale, la seconda stazione può essere saldata e la terza stazione può essere controllata e rimossa."
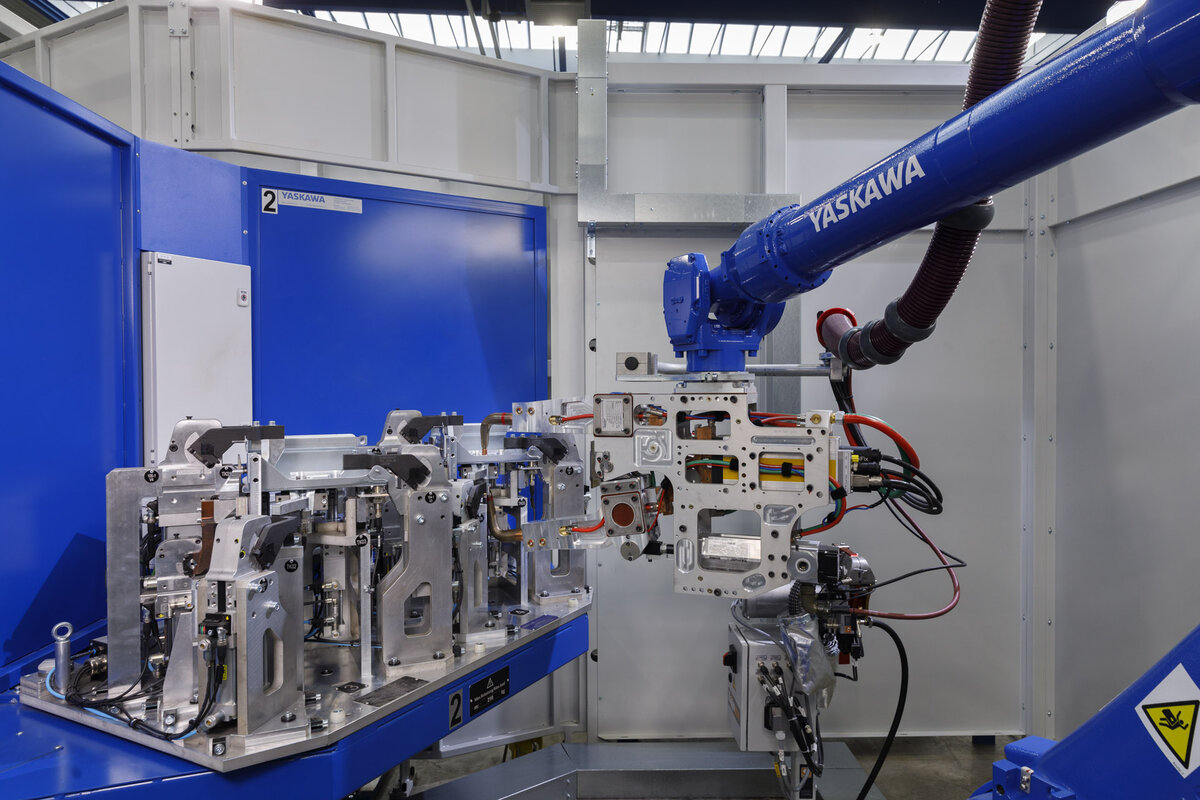
Una soluzione ben concepita
Il sistema recentemente commissionato convince grazie a molti dettagli ben studiati e requisiti di spazio limitati. Va da sé che ogni componente è stato selezionato tenendo conto di due fattori: massima prestazione e affidabilità.
Cominciando dai robot: la snella serie Motoman SP a sei assi e ad alte prestazioni si occupa della saldatura a punti, mentre un GP88 veloce e altrettanto preciso è responsabile dei processi di movimentazione. Thomas Pflüger afferma: "Non c'era molto da discutere nella scelta dei robot. Stiamo già utilizzando diversi robot Yaskawa e sappiamo soddisferanno le nostre esigenze al cento per cento. Dotati di elevata resistenza, questi robot sono altamente affidabili’.
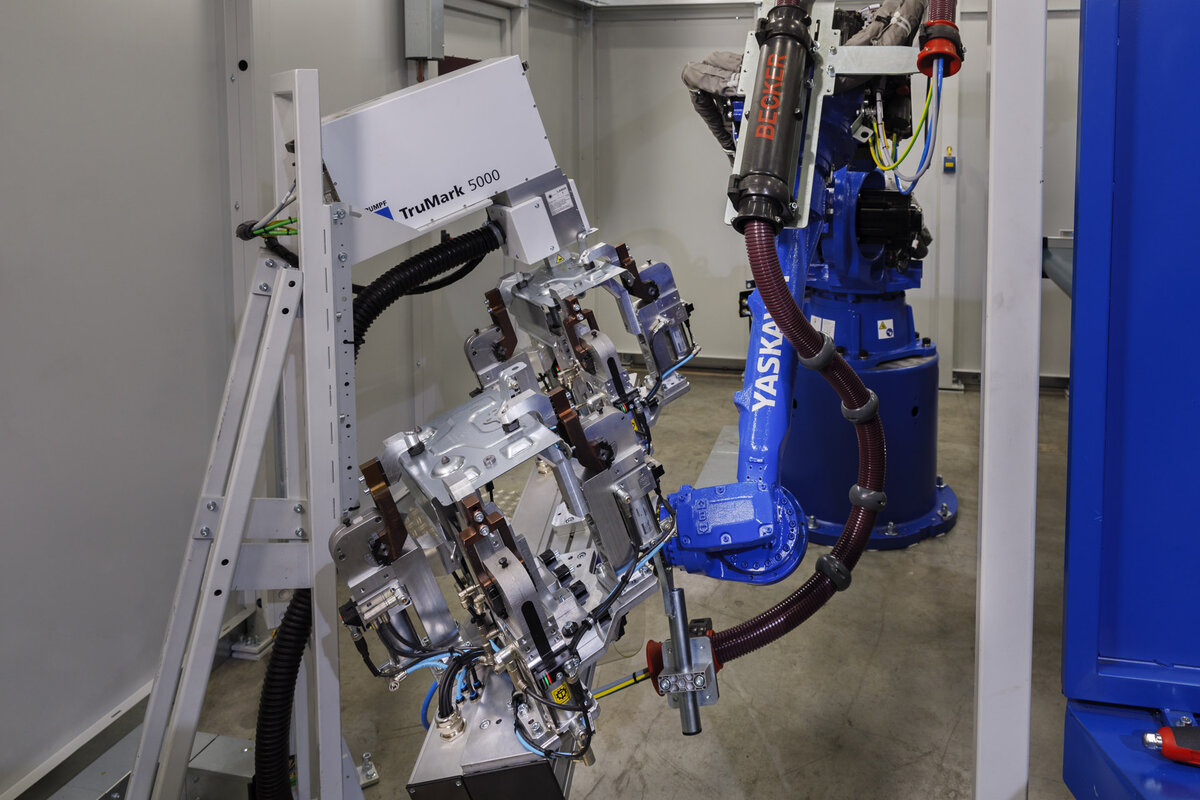
Progettato per la massima disponibilità
Grazie alla loro qualità, anche tutti gli altri componenti dovrebbero garantire un'elevata disponibilità. Sono in uso, tra gli altri, una pinza elettrica di saldatura leggera, una stazione automatica di pulizia e cambio per i cappucci degli elettrodi, un sistema di telecamere 2D di Cognex per la garanzia della qualità, un laser di marcatura di classe 1 di Trumpf, un PLC Siemens e un sistema di controllo della saldatura all'avanguardia di Bosch Rexroth con monitoraggio permanente dei parametri di saldatura.
Un punto di forza del sistema è il posizionatore verticale a 3 postazioni, dotato di due alloggiamenti per ogni postazione, per l'elaborazione parallela di sei telai delle batterie. Roland Hermann: "Ciò che lo rende speciale è che questa soluzione si basa su un prodotto standard Yaskawa, il posizionatore R-1000, che ha un asse di rotazione verticale. Abbiamo fornito questo azionamento di base modulare con una piastra di base progettata per dispositivi automatici ed eseguito la soluzione a tre stazioni. La rotazione di 120 gradi richiesta per l'applicazione è implementata in funzione esclusivamente da software. L'asse di posizionamento è integrato nel sistema di controllo principale del robot come un asse robotico completo."
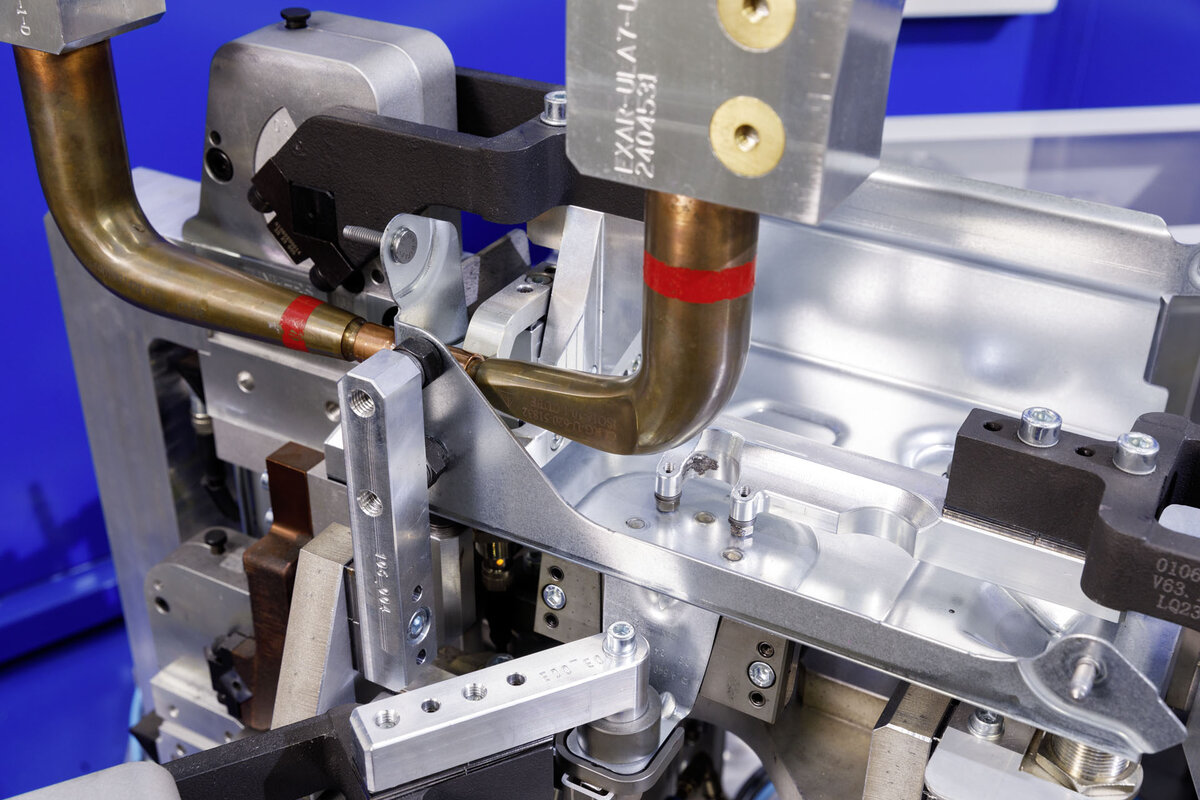
Pulizia e sostituzione dei cappucci degli elettrodi
Lo stato dei cappucci degli elettrodi è ovviamente decisivo per il processo. La pulizia regolare dei cappucci mediante fresatura dello strato di zinco risultante e la sostituzione dopo un numero specifico di operazioni di fresatura sono completamente automatiche alla stazione, senza l'intervento del l'operatore. Poiché questo è uno dei processi che determinano il tempo del ciclo, la posizione della stazione di pulizia e cambio è stata scelta per garantire lo spostamento più breve per il robot.
Una volta completata la saldatura a punti, il posizionatore scorre di nuovo di 120 gradi fino alla stazione tre. Qui la presenza e il corretto montaggio dei perni filettati e di un dado sono controllati dalla telecamera. Dopo aver superato i test QS, il robot Motoman GP88 con la sua doppia pinza pneumatica rimuove contemporaneamente entrambi i componenti e procede alla stazione di marcatura laser, dove i componenti ricevono un codice numerico letterale che serve per l'identificazione e la tracciabilità dei pezzi.
Durante l’implementazione si potrebbe fare a meno di speciali dispositivi aggiuntivi di protezione laser, in quanto i componenti vengono guidati dal robot di movimentazione alla testa di marcatura in modo sicuro per il laser. Ciò si ottiene applicando una pressione predefinita dal robot agli elementi di tenuta della testa di marcatura, realizzando così i requisiti per la sicurezza del laser. Nell'ultima fase, il robot a sei assi deposita le parti ideonee su un nastro trasportatore che viene scaricato manualmente. I componenti che la telecamera o il sistema di controllo della saldatura ritengono non idonei sono collocati dal robot di movimentazione in una scatola separata, controllata per quantità.
Il controllo generale del sistema è implementato da un PLC Siemens S7 di livello superiore con visualizzazione, al quale sono collegati i due controllori robot Yaskawa YRC 1000 tramite Profinet. Dopo la messa in servizio, il sistema ha funzionato senza problemi sia dal punto di vista del software sia dell'hardware.
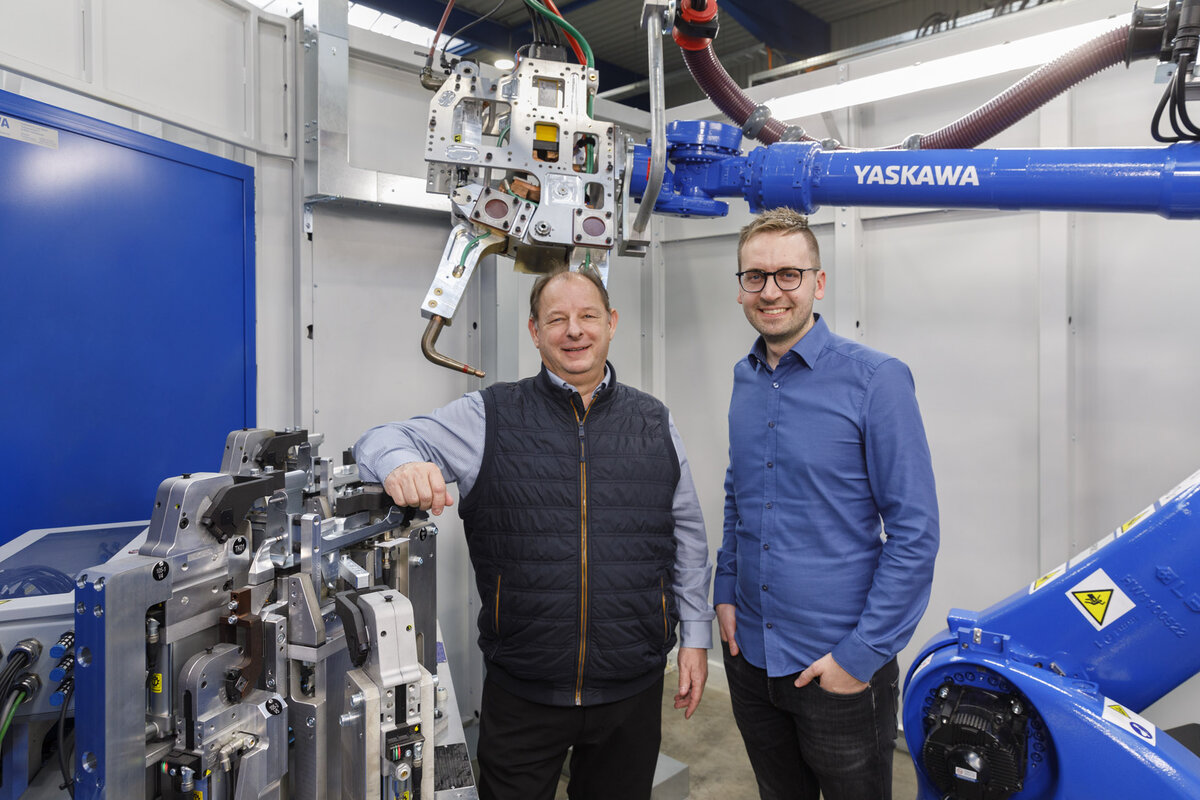
Picture: Roland Hermann (left), Yaskawa and Thomas Pflüger, Gebr. Binder are delighted about the successfully completed project.
Text: Ralf Högel
Pictures: YASKAWA Europe GmbH