Più di 100 anni di progresso tecnico ci hanno resi leader nei settori degli Inverter, dei servoazionamenti, della tecnologia di controllo e della robotica.
System integrator b-automated automates erosion machine with cobot from Yaskawa
Contract manufacturer Nordspan ventures into digital production
Contract manufacturers are specialists. That means they face very special challenges, for example in terms of skilled workers and efficient production processes. Like Nordspan GmbH: the young company from Schwentinental, Schleswig-Holstein, recently started addressing these challenges by embracing the opportunities presented by digitization. The prerequisite for this was an automation solution from system integrator b-automated with Yaskawa’s Cobot HC10DTP.
At least two reasons make the introduction of automation very attractive for smaller production companies. On the one hand, qualified professionals are today far too valuable to be used for monotonous or physically demanding activities. On the other hand, robots with the triumphant march of HRC-capable cobots are easier and more comfortable to use than ever before.
- Industrie
- Metallo
- Applicazioni
- Human-Robot Collaboration
- Machine Tending
- Material Handling
- Prodotti
- HC10DTP - Serie HC
Getting started in automation at Nordspan
Against this background, the decision makers at Nordspan GmbH in Schwentinental near Kiel also looked for new ways. The company – founded in 2019 – employs around 30 people, and is a contract manufacturer for its parent company JBS Systems, a leading manufacturer of flexible guide bushes and collets for automatic lathes. “Unfortunately, we are experiencing difficulties in finding qualified employees, so automation and digitalization are vital for us,” says CEO Maik Jeß.
For the first automation project, the choice fell on a wire eroding machine. Wire EDM is a process where the collets are precisely slotted, which takes up to an hour per work cycle. The process automation is correspondingly complex: the collets are processed under water. This requires a clamping device that has no problem with the process-related heavy soiling in the water. Furthermore, to prevent surface tarnishing the finished slotted pliers must be thoroughly cleaned and dried immediately after removal from the machine bed. In addition, the system should be easy to use and flexible, and fit into the confined working environment.
Picture: Heart of the complete solution for the automation of a wire EDM machine is a Yaskawa Cobot HC10DTP.
All-in-one solution from b-automated
In the search for the optimal concept for this challenging task, Yaskawa recommended that Nordspan contact system integrator b-automated and its owner Luciano Baumgart. The complete solution combines a ZeroCob modular system and clamping device from ZeroClamp with a Cobot HC10DTP and a gripper from Zimmer Group.
The interface between the robot control and the eroding machine is implemented via factory software from German provider software4production GmbH (abbreviated S4P). This also lays the foundation for further digitalization and automation with the goal of autonomous manufacturing. With the help of a web-based application, the plant network can now be monitored remotely to allow further optimization and ensure plant availability at the highest level in 24/7 operation.
Picture: Yaskawa Cobot HC10DTP with IP67 protection class.
Cobot HC10DTP
The heart of the cell is the cobot from the HC (human collaborative) series by Yaskawa. Although it is a full-fledged industrial robot, it can also work at a safely reduced speed. In the event of a collision – positively non-hazardous – the manipulator stops immediately. Thus there is no risk of injury to persons standing directly in its working area. At Nordspan, the robot is additionally secured by a surface safety scanner.
The selected cobot model offers a load capacity of 10 kg in combination with an effective range of 1200 mm, and convinces with its dust- and waterproof IP67 protection class. The Zimmer gripper is ideally matched to the manipulator. Specifically, it is a parallel gripper specially configured for the application with spring return. This prevents the component from falling out of the gripper, even in the event of pressure loss.
Like all models of the Motoman HC series, the HC10DTP features particularly user-friendly operation. In addition to the clearly arranged manual operating device, it is also possible to guide and program the robot arm directly by hand (direct teach, DT). This results in a time savings when creating robot programs.
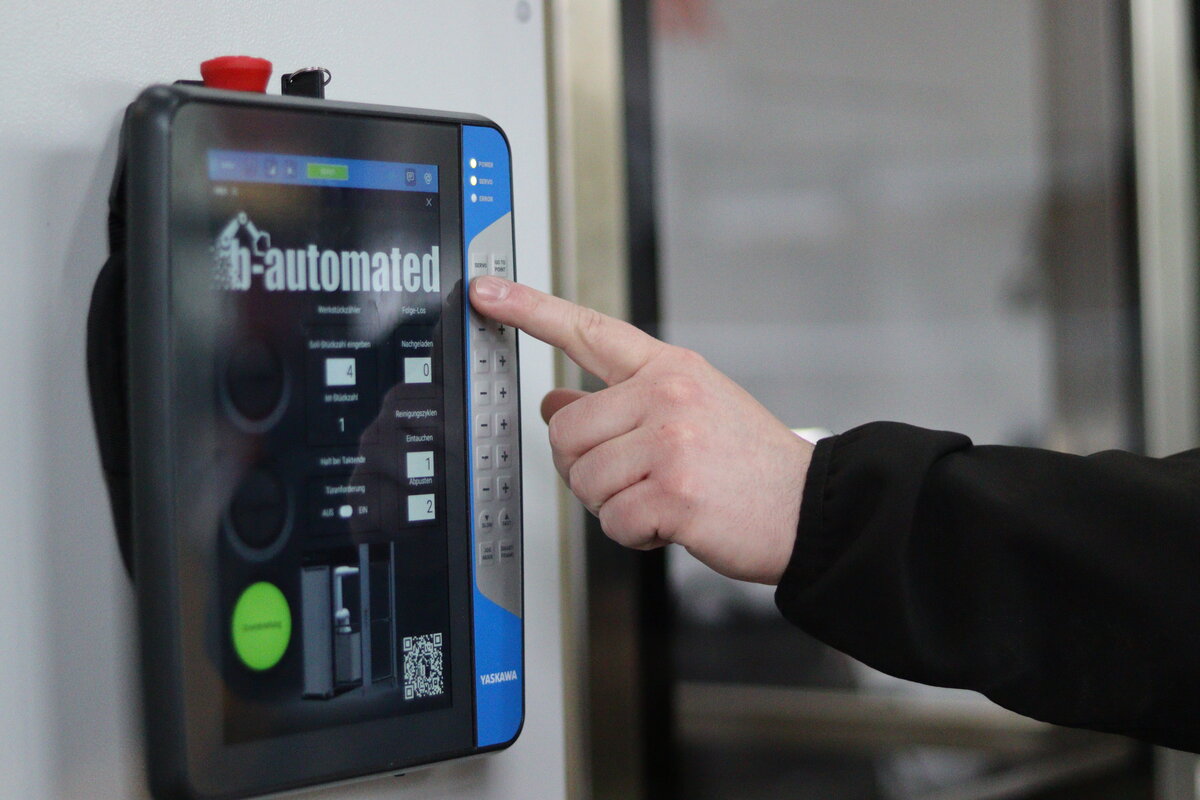
Picture: Operator interface of the system on the Smart pendant of the Yaskawa robot.
Practical experience
In total, the complete setup, assembly and integration of the robot – including peripherals with mechanics, electrics and software – took less than five working days. And since then, the system has more than proved its worth, as confirmed by Christian Wiese, machine operator at Nordspan: “The robot is very easy to use and does away with the monotonous work on the EDM machine! Now I can finally take care of more important things, and the robot colleague operates independently 7/24. What more could you want?” says the practitioner.
Thanks to the new automation, the wire EDM machine can also be operated autonomously in ‘ghost’ shifts, and achieves a completely unmanned autonomy time of almost 24 hours. Should a fault occur, this is always visible to the employees via an intuitive user interface and can be quickly dealt with, thus avoiding wasting precious machine time.
Nordspan’s managing director Maik Jeß expresses his satisfaction: “The robot cell will pay for itself in less than a year, and machine utilization has already more than doubled. That’s how it has to be!”
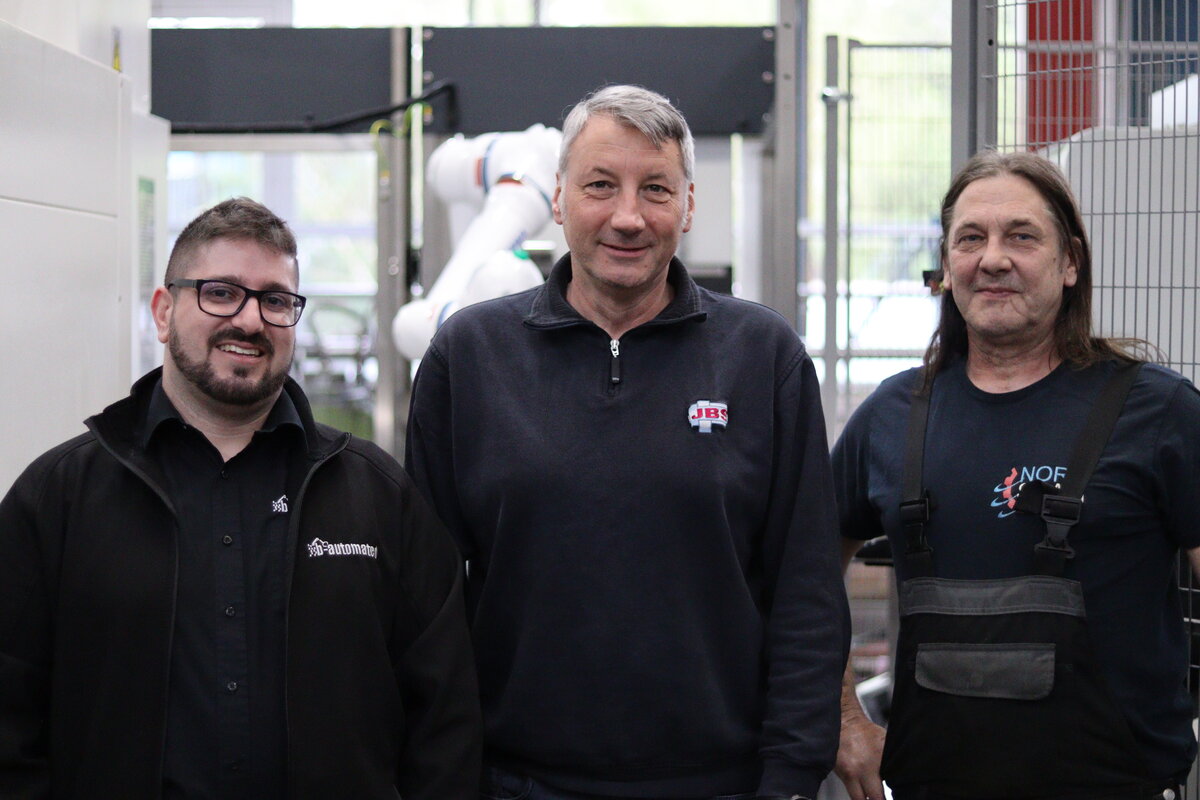
Picture: Successful entry into robotics (from left): Luciano Baumgart (b-automated), with Maik Jeß and Christian Wiese (both Nordspan)
Author:
Markus Schulz, Sales Manager Cobots
Yaskawa Europe GmbH – Robotics Division, DE-Allershausen
Contact for readers’ enquiries:
Tel.: +49-8166-90-0
robotics@yaskawa.eu
Source for all: b-automated Luciano Baumgart
Contact for the press:
Marion Annutsch
Marketing / PR / Communications
Yaskawa Europe GmbH
Tel.: +49-8166-90-0
marion.annutsch@yaskawa.eu
www.yaskawa.eu.com